According to data, the first baby stroller was born in England in 1733. At that time, it was just a stroller with a basket similar to a carriage. After the 20th century, baby strollers became popular, and their basic materials, platform structure, safety performance and other aspects are also constantly improving. Nowadays, baby strollers have basically become a must-have for families, and the inspection of baby strollers is particularly important.
Different countries have different inspection standards and methods for products such as baby strollers. The following are common inspection requirements for baby strollers.
Baby stroller inspection requirements
1. Color matching check
2. Product specification inspection
3. Appearance inspection (plastic appearance, hardware appearance, pipe fitting appearance)
4. Finished product structure testing requirements
5. Requirements for component and rivet combinations
6. Requirements for lathe function inspection
7. Parasol inspection requirements
8. Packaging inspection requirements
The color matching is correct and meets the requirements of the order information. There is no wrong color or style.
2. Product specification inspection
1). Product specifications must be consistent with engineering and technical data;
2). Bulk goods must match the limited sample.
3. Appearance inspection (plastic appearance, hardware appearance, pipe fitting appearance)
1). No orange peel, yellowing, delamination, blistering or burning;
2). No thick or thin wall phenomenon;
3). No dents or distortions;
4). Cut off the mold closing line and make it smooth;
5). The surface is bright and the color is uniform without impurities and color difference;
6). No scratches, rust, blistering, delamination, pinholes, cracking or peeling;
7). No forming edges and sharp points;
8). No dents, distortions, deformations, etc.;
9). No desoldering, missing soldering, bubbles, uneven welding, etc.
4. Finished product structure testing requirements
1). The brakes and removable parts operate normally and there is no failure;
2). The width of the platform is consistent with the design width: ±1.0mm;
3). Walking in a straight line: Sliding 5 meters from a 10-degree slope, with no deviation of 0.3 meters from left to right (reference standard JIS0294);
4). Passed the one-point, three-line and six-sided box dropping test;
5). Pass the front wheel lifting weight test (according to regional standards and customer requirements);
6). Push up and down test on the stroller handle (reference standard GB 14748)
Handlebar strength test method: Place the corresponding number of test weights in the sleeping bag and secure it with a safety belt. In a controlled manner, alternately raise or lower the handlebars so that the front and rear wheels are lifted by 120mm±10mm in turn. (As shown in the figure), and tested 800 times at a frequency of 15 cycles/min±2 cycles/min. For reversible handlebars, the test shall be conducted 400 times in each direction. If the handlebar has an adjustable device, the test shall be carried out under the most adverse conditions.
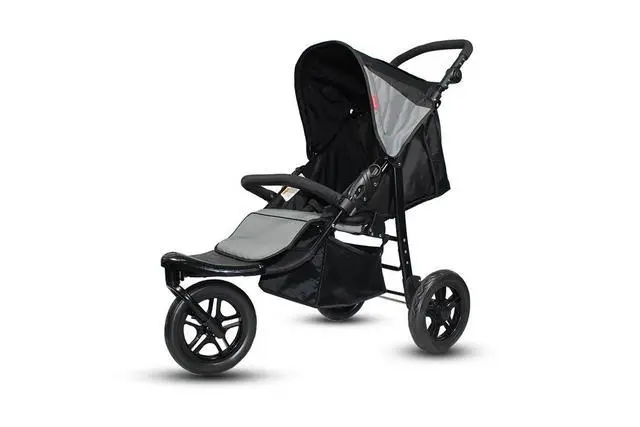
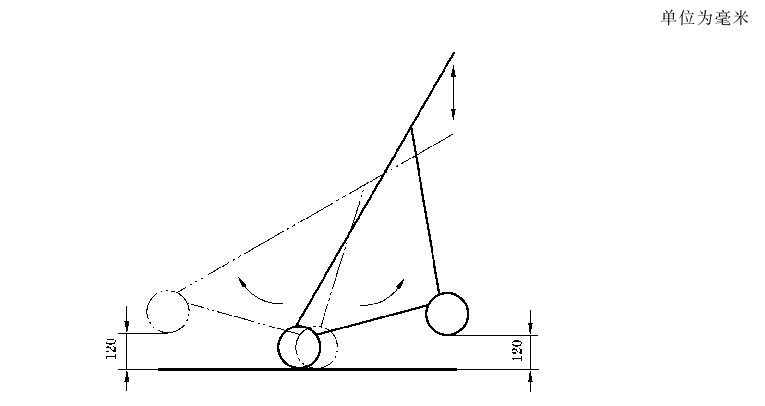
7). Cart impact strength test (reference standard GB 14748)
Impact strength test method: Place the corresponding number of test weights in the sleeping bag, secure it with a seat belt, place the vehicle on a 10° ramp, release the vehicle 1000mm away from the stop and let it drive down the ramp freely, and impact to a rigid stop whose height should be at least half the diameter of the wheel. Repeat the test a total of 10 times.
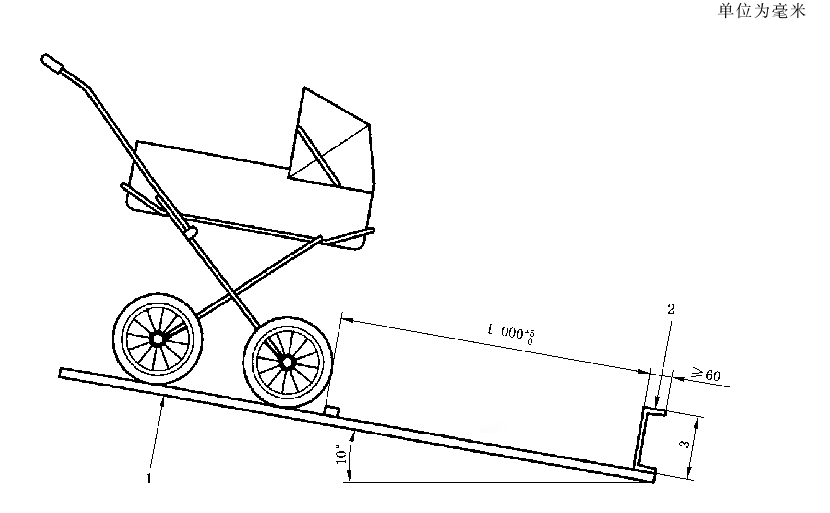
1-hard platform;
2-steel stop;
3-The height of the stop, at least half the diameter of the wheel.
5. Requirements for component and rivet combinations
1). The rivet back opening is 2~3mm and is complete without plating delamination;
2). Appropriate tightness, no bending or sharp edges;
3). The male and female screws are locked in place without sharp burrs;
4). Combined fastening and flexible rotation; the gap between the front and rear wheels is 1.0~1.5mm;
5). The self-tapping screws are locked in place and cannot be loosened;
6). The sticker is in the correct position and has no blisters, corners or tatters;
7). The left and right parts and directional parts should be combined according to the requirements and limited samples of the work instructions, and should not be confused or reversed;
8). If jigs are used, they must be able to be easily inserted into the inspection jigs.
6. Requirements for lathe function inspection
1). The front and rear wheels must rotate flexibly. If the front wheels can be oriented, they must be firmly engaged;
2). All lathes with two locks must be locked firmly and cannot be detached;
3). If there is a reversing handle, the reversing spirit must be locked in place and firmly;
4). The contact surface between the wheel and the brake teeth is at least 5mm, and they must be firmly engaged and not disengaged;
5). The backrest adjustment should withstand a force of 15 kilograms without automatically sliding down, and the backrest adjustment should be smooth and not sluggish;
6). The pedal adjustment must be smooth;
7). The front armrest is installed smoothly and snaps firmly.
7. Parasol inspection requirements
1). There are no foreign objects in the hemming and stitching on the parasol, and there are no broken threads, dirt, skipped stitches, holes, etc.;
2). The closing function of the parasol is not too tight or loose;
3). Open the mesh with your hands to make sure there are no tears;
4). Make sure that the functional buckle on the parasol functions normally, and there are no problems such as seamless reverse, wrong model, etc.
8. Packaging inspection requirements
1). The contents of carton marks and stickers must be correct, and there must be no missing prints, misprints, blurs or misalignments;
2). The packaging method must be in accordance with engineering and technical requirements;
3). Packaging PE bags must have ventilation holes and warnings printed on them;
4). Warning stickers must be printed on one side of the carriage;
5). The backrest and seat belt must have warning labels sewn on them;
6). The woven label and LOGO printed on the machine must be clear and not fall off, and printed in the specified position;
7). Packaging parts must not be misplaced, including instructions, warranty cards, etc., which must comply with the engineering packaging picture requirements;
8). The packaging box should be flat and should not be cracked or dirty;
9). The sealing of the box must be smooth and firm, and the lid cannot be easily detached.
In addition, each country has classified the use nature of products such as strollers sold in the country and formulated targeted standards for safety control. The following are the safety testing standards for strollers in various countries:
(1) China - GB14747 This standard applies to children's tricycles for one or more children.
(2) China - GB 14749 This standard applies to baby walkers used by babies from the age of being able to sit up to being able to walk on their own.
(3) China - GB 14748 This standard applies to children's wheeled strollers for one child or multiple children.
(4) United States - ASTM F977 This standard applies to baby walkers used by infants.
(5) United States - ASTM F833 This standard applies to wheeled strollers for carrying infants or children.
(6) European Union - EN 1273/BS EN1273 This standard applies to baby walkers used by babies from being able to sit up to being able to walk on their own.
(7) European Union - EN 1888 This standard applies to children's wheeled strollers for one child or multiple children.
(8) Australia/New Zealand—AS/NZS 2088 This standard applies to wheeled strollers for carrying infants or children.
Reference Information:
National Standard: Safety Requirements for Children’s Strollers (GB 14748-2006)
Post time: Mar-20-2024