The appearance quality of a product is an important aspect of sensory quality. Appearance quality generally refers to the quality elements of a product's shape, color tone, luster, pattern, and other visual observations.
Obviously, all defects such as bumps, scratches, indentations, scratches, rust, mold, bubbles, pinholes, pits, surface cracks, delamination, wrinkles, etc. will have an impact on the appearance quality of the product. In addition, many appearance product quality factors directly affect product performance, lifespan, and other aspects. Products with smooth surfaces have strong rust resistance, low friction coefficient, good wear resistance, and low energy consumption.
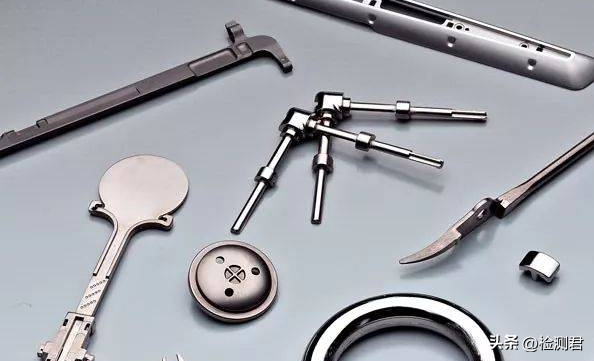
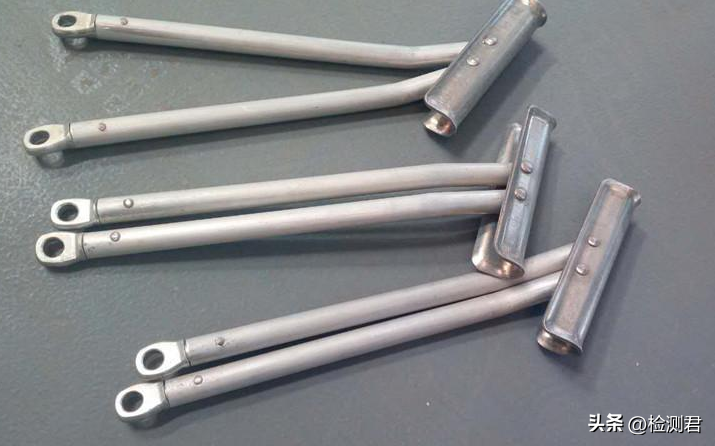
The evaluation of product appearance quality has a certain degree of subjectivity. In order to make objective judgments as much as possible, the following inspection methods are often used in industrial product quality inspection.
(1) Standard sample group method. Pre select qualified and unqualified samples as standard samples, where unqualified samples have various defects with varying degrees of severity.
The standard sample can be repeatedly observed by many inspectors (evaluators) and the observation results can be statistically analyzed. After analyzing the statistical results, it is possible to determine which defect categories are improperly specified; Which inspectors do not have a deep understanding of the standards; Which inspectors lack the necessary training and discernment skills.
(2) Photo observation method. Through photography, qualified appearance and allowable defect limits can be represented by photos, and typical photos of various impermissible defects can also be used for comparative inspection.
(3) Defect amplification method. Use a magnifying glass or projector to magnify the surface of the product and search for defects on the observed surface, in order to accurately determine the nature and severity of the defects.
(4) Disappearance distance method. Go to the product usage site, inspect the product's usage conditions, and observe the product's usage status. Then simulate the actual usage conditions of the product, and specify the corresponding time, observation distance, and angle as observation conditions for inspection. For example, if a certain product's appearance defect cannot be seen within 3 seconds from a distance of one meter, it is considered qualified, otherwise it is considered unqualified. This method is much more convenient and applicable than setting standards item by item based on various types and severity of appearance defects, and conducting inspections item by item.
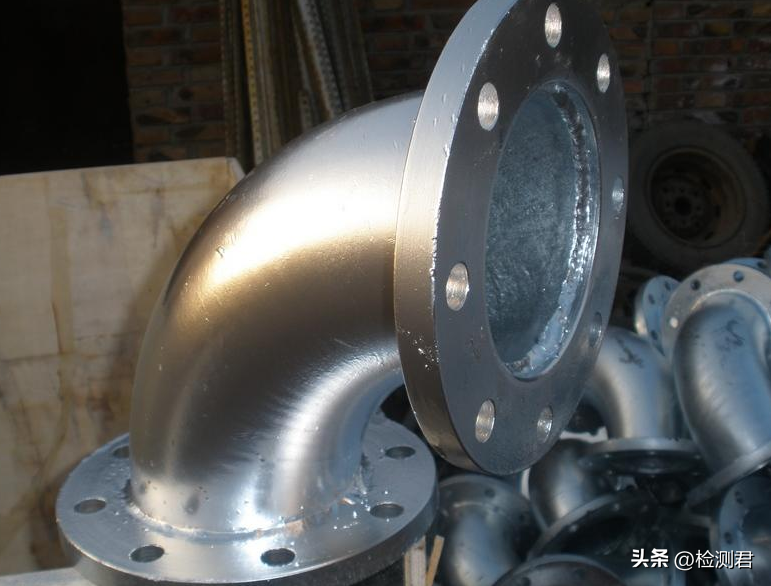
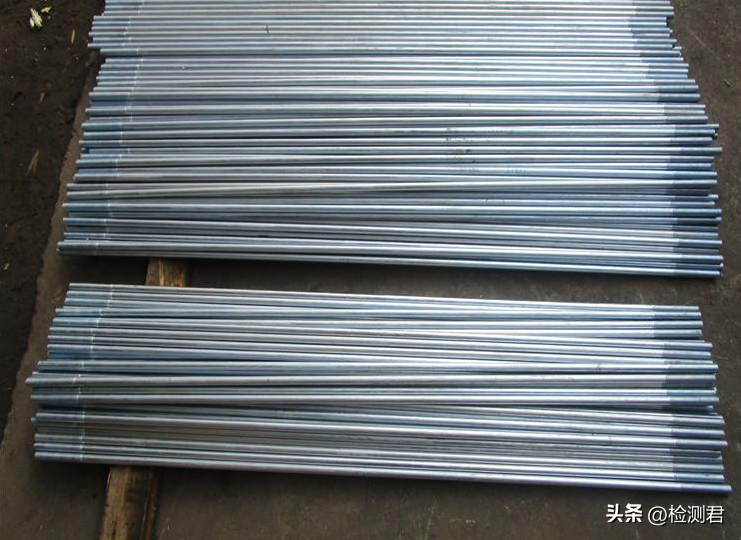
Example: Appearance quality inspection of galvanized coating on components.
① Appearance quality requirements. The appearance quality of the galvanized layer includes four aspects: color, uniformity, allowable defects, and non allowable defects.
Color. For example, the galvanized layer should be a light gray with a slight beige color; After being exposed to light, the galvanized layer becomes a silver white with a certain luster and a slight hint of light blue; After phosphate treatment, the galvanized layer should be light gray to silver gray.
Uniformity. The galvanized layer is required to have a finely crystallized, uniform, and continuous surface.
Permissible defects. For example, slight water marks; Slight fixture marks on the surface of very important parts; There are slight differences in color and gloss on the same part.
No defects allowed. For example, blistering, peeling, burning, nodulation, and pitting of the coating; Dendritic, spongy, and striped coatings; Uncleaned salt stains, etc.
② Sampling for appearance inspection. For important parts, critical parts, large parts, and ordinary parts with a batch size of less than 90 pieces, the appearance should be inspected 100% to eliminate non-conforming products; For ordinary parts with a batch size greater than 90 pieces, sampling inspection should be carried out, with a general inspection level of II and a qualified quality level of 1.5%. The inspection should be carried out according to the normal inspection sampling plan specified in Table 2-12. When a non-conforming batch is found, it is allowed to conduct a 100% inspection of the batch, eliminate the non-conforming products, and resubmit for inspection.
③ Appearance inspection methods and quality evaluation. Visual inspection is the main method for appearance inspection, and if necessary, 3-5 times magnifying glass can be used for inspection. During inspection, natural scattered light or white transmitted light without reflected light shall be used. The illuminance shall not be less than 300 Lux, and the distance between parts and human eyes shall be 250 mm. If the batch size is 100, a sample size of 32 pieces can be selected; Through visual inspection of these 32 pieces, it was found that two of them had blisters on the coating and burnt marks. Due to the number of non-conforming products being 2, this batch of parts was deemed unqualified.
Post time: Aug-01-2023