తేలికపాటి మరియు సన్నని బట్టలు అధిక ఉష్ణోగ్రతలు ఉన్న ప్రాంతాలు మరియు వాతావరణాలలో ఉపయోగించడానికి ప్రత్యేకంగా సరిపోతాయి.సాధారణ ప్రత్యేక కాంతి మరియు సన్నని బట్టలలో పట్టు, షిఫాన్, జార్జెట్, గ్లాస్ నూలు, ముడతలు, లేస్ మొదలైనవి ఉన్నాయి. ఇది శ్వాసక్రియ మరియు సొగసైన అనుభూతి కోసం ప్రపంచవ్యాప్తంగా ఉన్న ప్రజలచే ఇష్టపడబడుతుంది మరియు నా దేశం యొక్క ఎగుమతులలో అధిక భాగాన్ని కలిగి ఉంది.
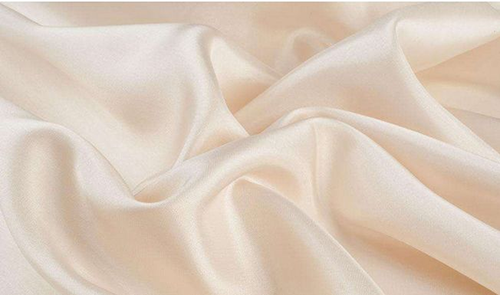
కాంతి మరియు సన్నని బట్టల ఉత్పత్తిలో ఏ సమస్యలు సంభవించవచ్చు మరియు వాటిని ఎలా ఎదుర్కోవాలి?కలిసి దాన్ని క్రమబద్ధీకరించుదాం.
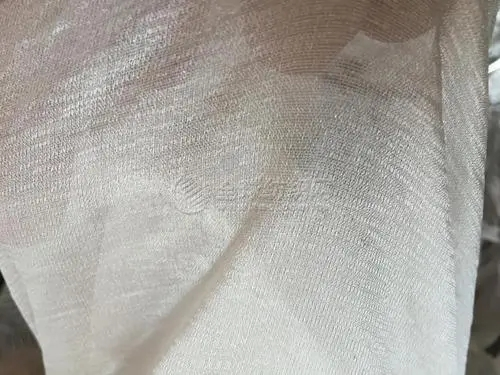
కారణ విశ్లేషణ: సీమ్ ముడతలు నేరుగా వస్త్రాల నాణ్యతను ప్రభావితం చేస్తాయి.సాధారణ కారణాలు అధిక సీమ్ టెన్షన్ వల్ల ఏర్పడే సీమ్ సంకోచం, అసమాన ఫాబ్రిక్ ఫీడింగ్ వల్ల సీమ్ కుంచించుకుపోవడం మరియు ఉపరితల ఉపకరణాల అసమాన సంకోచం వల్ల ఏర్పడే సీమ్ సంకోచం.ముడతలు.
ప్రక్రియ పరిష్కారాలు:
కుట్టు ఒత్తిడి చాలా గట్టిగా ఉంది:
① కుట్టు థ్రెడ్, బాటమ్ లైన్ మరియు ఫాబ్రిక్ మరియు ఓవర్లాక్ థ్రెడ్ మధ్య టెన్షన్ను వీలైనంత వరకు విప్పుటకు ప్రయత్నించండి;
② కుట్టు సాంద్రతను తగిన విధంగా సర్దుబాటు చేయండి మరియు కుట్టు సాంద్రత సాధారణంగా అంగుళానికి 10-12 అంగుళాలకు సర్దుబాటు చేయబడుతుంది.సూది.
③ఇలాంటి ఫాబ్రిక్ ఎలాస్టిసిటీ లేదా చిన్న స్ట్రెచ్ రేట్లతో కుట్టు దారాలను ఎంచుకోండి మరియు షార్ట్ ఫైబర్ కుట్టు దారాలు లేదా సహజ ఫైబర్ కుట్టు థ్రెడ్లు వంటి మృదువైన మరియు సన్నని థ్రెడ్లను ఉపయోగించడానికి ప్రయత్నించండి.
ఉపరితల ఉపకరణాల అసమాన సంకోచం:
① ఉపకరణాలను ఎంచుకున్నప్పుడు, ఫైబర్ కూర్పు మరియు సంకోచం రేటుకు ప్రత్యేక శ్రద్ధ ఉండాలి, ఇది ఫాబ్రిక్ యొక్క లక్షణాలకు అనుగుణంగా ఉండాలి మరియు సంకోచం రేటులో వ్యత్యాసం 1% లోపల నియంత్రించబడాలి.
② ఉత్పత్తిలో పెట్టడానికి ముందు, కుంచించుకుపోయే రేటును తెలుసుకోవడానికి మరియు సంకోచం తర్వాత రూపాన్ని గమనించడానికి ఫాబ్రిక్ మరియు ఉపకరణాలు ముందుగా కుదించబడాలి.
2. నూలు గీయండి
కారణ విశ్లేషణ: కాంతి మరియు సన్నని బట్టల నూలు సన్నగా మరియు పెళుసుగా ఉన్నందున, అధిక-వేగంతో కుట్టు ప్రక్రియలో, మొద్దుబారిన ఫీడ్ పళ్ళు, ప్రెజర్ పాదాలు, మెషిన్ సూదులు, సూది ప్లేట్ రంధ్రాలు మొదలైన వాటి ద్వారా ఫైబర్లు సులభంగా కట్టిపడేస్తాయి. లేదా యంత్రం సూది ద్వారా వేగంగా మరియు తరచుగా పంక్చర్ల కారణంగా.కదలిక నూలును గుచ్చుతుంది మరియు చుట్టుపక్కల ఉన్న నూలును బిగించి, సాధారణంగా "డ్రాయింగ్ నూలు" అని పిలుస్తారు.ఉదాహరణకు, డోర్-కటింగ్ మెషీన్పై బ్లేడ్తో బటన్హోల్స్ను గుద్దేటప్పుడు, బటన్హోల్స్ చుట్టూ ఉన్న ఫైబర్లు తరచుగా బ్లేడ్ల ద్వారా బయటకు తీయబడతాయి.తీవ్రమైన సందర్భాల్లో, నూలు నిర్లిప్తత లోపాలు సంభవించవచ్చు.
ప్రక్రియ పరిష్కారాలు:
① మెషిన్ సూది ఫాబ్రిక్ దెబ్బతినకుండా నిరోధించడానికి, ఒక చిన్న సూదిని ఉపయోగించాలి.అదే సమయంలో, ఒక రౌండ్ చిట్కాతో సూదిని ఎంచుకోవడానికి శ్రద్ద.తేలికపాటి మరియు సన్నని బట్టలకు అనువైన అనేక సూది నమూనాలు క్రిందివి:
జపనీస్ సూది: సూది పరిమాణం 7~12, S లేదా J-ఆకారపు సూది చిట్కా (అదనపు చిన్న గుండ్రని తల సూది లేదా చిన్న గుండ్రని తల సూది);
B యూరోపియన్ సూది: సూది పరిమాణం 60 ~ 80, స్పై చిట్కా (చిన్న రౌండ్ తల సూది);
సి అమెరికన్ సూది: సూది పరిమాణం 022~032, బాల్ చిట్కా సూది (చిన్న గుండ్రని తల సూది)
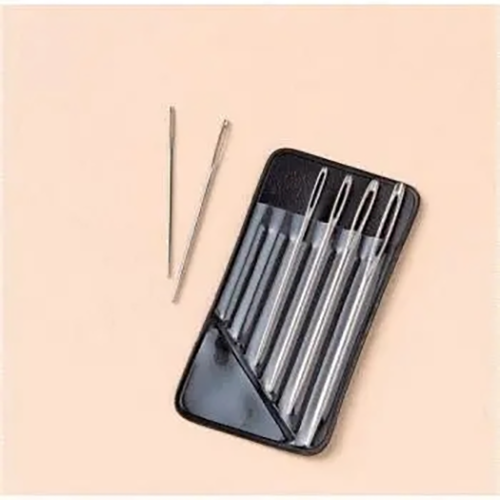
② సూది ప్లేట్ రంధ్రం యొక్క పరిమాణాన్ని సూది నమూనాకు అనుగుణంగా మార్చాలి.కుట్టు సమయంలో స్టిచ్ స్కిప్పింగ్ లేదా థ్రెడ్ డ్రాయింగ్ వంటి సమస్యలను నివారించడానికి చిన్న-పరిమాణ సూదులను చిన్న రంధ్రాలతో సూది ప్లేట్లతో భర్తీ చేయాలి.
③ప్లాస్టిక్ ప్రెస్సర్ పాదాలతో భర్తీ చేయండి మరియు ప్లాస్టిక్ అచ్చులతో కప్పబడిన కుక్కలకు ఆహారం ఇవ్వండి.అదే సమయంలో, గోపురం ఆకారంలో ఉండే ఫీడ్ డాగ్లను ఉపయోగించడం మరియు మొద్దుబారిన ఫీడ్ భాగాలను సకాలంలో భర్తీ చేయడం మొదలైన వాటిపై శ్రద్ధ వహించండి, ఇవి కత్తిరించిన ముక్కలను సాఫీగా రవాణా చేయగలవు మరియు నూలు డ్రా మరియు స్నాగ్ చేయడం మరియు దెబ్బతినడం వంటి సమస్యలను తగ్గించగలవు. ఫాబ్రిక్ ఏర్పడుతుంది.
④ కత్తిరించిన ముక్క యొక్క అంచుకు జిగురును వర్తింపజేయడం లేదా అంటుకునే లైనింగ్ను జోడించడం వల్ల కుట్టుపని కష్టాన్ని తగ్గించవచ్చు మరియు కుట్టు యంత్రం వల్ల నూలుకు కలిగే నష్టాన్ని తగ్గించవచ్చు.
⑤ స్ట్రెయిట్ బ్లేడ్ మరియు నైఫ్ రెస్ట్ ప్యాడ్తో బటన్ డోర్ మెషీన్ను ఎంచుకోండి.బటన్హోల్ను తెరవడానికి బ్లేడ్ మూవ్మెంట్ మోడ్ క్షితిజ సమాంతర కట్టింగ్కు బదులుగా క్రిందికి గుద్దడాన్ని ఉపయోగిస్తుంది, ఇది నూలు డ్రాయింగ్ సంభవించడాన్ని సమర్థవంతంగా నిరోధించగలదు.
కారణ విశ్లేషణ: సీమ్ గుర్తులలో రెండు సాధారణ రకాలు ఉన్నాయి: "సెంటిపెడ్ మార్కులు" మరియు "టూత్ మార్కులు."కుట్లు కుట్టిన తర్వాత బట్టపై నూలును పిండడం వల్ల "సెంటిపెడ్ మార్కులు" ఏర్పడతాయి, దీని వలన కుట్టు ఉపరితలం అసమానంగా ఉంటుంది.కాంతి ప్రతిబింబం తర్వాత నీడలు చూపబడతాయి;ఫీడ్ డాగ్లు, ప్రెస్సర్ పాదాలు మరియు సూది ప్లేట్లు వంటి ఫీడింగ్ మెషీన్ల ద్వారా సన్నని, మృదువైన మరియు తేలికపాటి బట్టల సీమ్ అంచులు గీతలు లేదా గీతలు పడటం వల్ల "పళ్ళ గుర్తులు" ఏర్పడతాయి.ఒక స్పష్టమైన ట్రేస్.
"సెంటిపెడ్ నమూనా" ప్రక్రియ పరిష్కారం:
① ఫాబ్రిక్పై అనేక వరుసల ముడతలు పడిన శైలులను నివారించేందుకు ప్రయత్నించండి, స్ట్రక్చరల్ లైన్లను కత్తిరించడానికి పంక్తులను తగ్గించండి లేదా ఉపయోగించవద్దు, కత్తిరించాల్సిన భాగాలలో నేరుగా మరియు క్షితిజ సమాంతర రేఖలకు బదులుగా వికర్ణ రేఖలను ఉపయోగించడాన్ని పరిగణించండి మరియు నేరుగా ధాన్యాల దిశలో కత్తిరించకుండా ఉండండి. దట్టమైన కణజాలంతో.పంక్తులు కట్ మరియు ముక్కలు సూది దారం ఉపయోగించు.
② స్థలం మొత్తాన్ని తగ్గించండి లేదా పెంచండి: ముడి అంచులను ప్రాసెస్ చేయడానికి సాధారణ సీమ్ మడతను ఉపయోగించండి మరియు అలంకార టాప్స్టిచ్ను నొక్కకుండా లేదా తక్కువ నొక్కకుండా, ఒకే లైన్తో ఫాబ్రిక్ను కుట్టండి.
③బట్టలను రవాణా చేయడానికి నీడిల్ ఫీడ్ పరికరాన్ని ఉపయోగించవద్దు.డబుల్-నీడిల్ మెషీన్లు సూది ఫీడ్ పరికరాలతో అమర్చబడి ఉంటాయి కాబట్టి, టాప్స్టిచింగ్ యొక్క డబుల్ వరుసలను క్యాప్చర్ చేయడానికి మీరు డబుల్-నీడిల్ మెషీన్లను ఉపయోగించకుండా ఉండాలి.స్టైల్ డబుల్-రో టాప్స్టిచింగ్ను క్యాప్చర్ చేయడానికి డిజైన్ను కలిగి ఉంటే, మీరు డబుల్ థ్రెడ్లను విడిగా క్యాప్చర్ చేయడానికి సింగిల్-నీడిల్ కుట్టు యంత్రాన్ని ఉపయోగించవచ్చు.
④ ఫాబ్రిక్ అలల రూపాన్ని తగ్గించడానికి ముక్కలను ట్విల్ లేదా నేరుగా వికర్ణ దిశలో కత్తిరించడానికి ప్రయత్నించండి.
⑤కుట్టు దారం ఆక్రమించిన స్థలాన్ని తగ్గించడానికి తక్కువ నాట్లు మరియు సున్నితత్వంతో సన్నని కుట్టు దారాన్ని ఎంచుకోండి.స్పష్టమైన పొడవైన కమ్మీలతో ప్రెస్సర్ ఫుట్ ఉపయోగించవద్దు.ఫాబ్రిక్ నూలుకు మెషిన్ సూది యొక్క నష్టాన్ని తగ్గించడానికి చిన్న గుండ్రని-నోరు యంత్ర సూది లేదా చిన్న-రంధ్ర యంత్ర సూదిని ఎంచుకోండి.
⑥ నూలు స్క్వీజింగ్ను తగ్గించడానికి ఫ్లాట్ స్టిచ్కి బదులుగా ఐదు-థ్రెడ్ ఓవర్లాకింగ్ పద్ధతి లేదా చైన్ స్టిచ్ని ఉపయోగించండి.
⑦బట్టల మధ్య దాగి ఉన్న కుట్టు దారాన్ని తగ్గించడానికి కుట్టు సాంద్రతను సర్దుబాటు చేయండి మరియు థ్రెడ్ టెన్షన్ను విప్పు.
"ఇండెంట్" ప్రక్రియ పరిష్కారాలు:
①ప్రెజర్ పాదాల ఒత్తిడిని తగ్గించండి, డైమండ్ ఆకారంలో లేదా గోపురం ఉన్న ఫైన్ ఫీడ్ పళ్లను ఉపయోగించండి, లేదా ప్లాస్టిక్ ప్రెస్సర్ ఫుట్ మరియు ఫీడర్ ద్వారా ఫాబ్రిక్కు జరిగే నష్టాన్ని తగ్గించడానికి రబ్బర్ ప్రొటెక్టివ్ ఫిల్మ్తో పళ్లను ఫీడ్ చేయండి.
② ఫీడ్ డాగ్ మరియు ప్రెస్సర్ ఫుట్ నిలువుగా సర్దుబాటు చేయండి, తద్వారా ఫీడ్ డాగ్ మరియు ప్రెస్సర్ ఫుట్ యొక్క శక్తులు సమతుల్యంగా ఉంటాయి మరియు ఫాబ్రిక్ దెబ్బతినకుండా ఒకదానికొకటి ఆఫ్సెట్ చేయబడతాయి.
③ సీమ్ అంచులకు జిగురు లైనింగ్, లేదా గుర్తులు కనిపించే అవకాశం ఉన్న సీమ్లపై కాగితాన్ని ఉంచండి, గుర్తుల రూపాన్ని తగ్గించండి.
కారణ విశ్లేషణ: కుట్టు యంత్రం యొక్క వదులుగా ఉండే గుడ్డ ఫీడింగ్ భాగాల కారణంగా, క్లాత్ ఫీడింగ్ ఆపరేషన్ అస్థిరంగా ఉంటుంది మరియు ప్రెస్సర్ ఫుట్ యొక్క ఒత్తిడి చాలా వదులుగా ఉంటుంది.ఫాబ్రిక్ యొక్క ఉపరితలంపై కుట్లు వక్రంగా మరియు చలించటానికి అవకాశం ఉంది.కుట్టు యంత్రాన్ని తీసివేసి, మళ్లీ కుట్టినట్లయితే, సూది రంధ్రాలు సులభంగా వదిలివేయబడతాయి, ఫలితంగా ముడి పదార్థాలు వృధా అవుతాయి..
ప్రక్రియ పరిష్కారాలు:
①ఒక చిన్న సూది మరియు చిన్న రంధ్రాలతో ఒక సూది ప్లేట్ ఎంచుకోండి.
② ఫీడ్ డాగ్ యొక్క స్క్రూలు వదులుగా ఉన్నాయో లేదో తనిఖీ చేయండి.
③స్టిచ్ టెన్షన్ను కొంచెం బిగించి, కుట్లు యొక్క సాంద్రతను సర్దుబాటు చేయండి మరియు ప్రెస్సర్ ఫుట్ యొక్క టెన్షన్ను పెంచండి.
కారణ విశ్లేషణ: కుట్టు సమయంలో కుట్టు యంత్రం ఆపివేయబడినప్పుడు, నూనె త్వరగా ఆయిల్ పాన్కి తిరిగి వెళ్లదు మరియు కత్తిరించిన ముక్కలను కలుషితం చేయడానికి సూది పట్టీకి జోడించబడుతుంది.ముఖ్యంగా పలుచని సిల్క్ ఫ్యాబ్రిక్లు మెషిన్ టూల్ నుండి శోషించబడతాయి మరియు బయటకు వచ్చే అవకాశం ఉంది మరియు హై-స్పీడ్ కుట్టు మిషన్తో కుట్టినప్పుడు దంతాలకు ఆహారం ఇస్తుంది.చిందిన ఇంజిన్ ఆయిల్.
ప్రక్రియ పరిష్కారాలు:
① అద్భుతమైన చమురు రవాణా వ్యవస్థతో కూడిన కుట్టు యంత్రాన్ని లేదా ప్రత్యేకంగా రూపొందించిన సీల్డ్ ఆయిల్ ట్రాన్స్పోర్ట్ కుట్టు యంత్రాన్ని ఎంచుకోండి.ఈ కుట్టు యంత్రం యొక్క సూది పట్టీ మిశ్రమంతో తయారు చేయబడింది మరియు ఉపరితలంపై రసాయన ఏజెంట్ పొరతో పూత పూయబడింది, ఇది ఘర్షణ మరియు అధిక ఉష్ణోగ్రతను నిరోధించగలదు మరియు చమురు చిందటాన్ని సమర్థవంతంగా నిరోధించగలదు..ఆయిల్ డెలివరీ వాల్యూమ్ను మెషిన్ టూల్లో స్వయంచాలకంగా సర్దుబాటు చేయవచ్చు, కానీ ఖర్చు ఎక్కువగా ఉంటుంది.
② ఆయిల్ సర్క్యూట్ను క్రమం తప్పకుండా తనిఖీ చేయండి మరియు శుభ్రం చేయండి.కుట్టు యంత్రానికి నూనెను పూయేటప్పుడు, కేవలం సగం బాక్స్ నూనెను మాత్రమే నింపండి మరియు పంపిణీ చేయబడిన నూనె మొత్తాన్ని తగ్గించడానికి చమురు పైపు యొక్క థొరెటల్ను తగ్గించండి.చమురు చిందటం నిరోధించడానికి ఇది కూడా సమర్థవంతమైన సాంకేతికత.
③వాహనం వేగాన్ని తగ్గించడం వల్ల ఆయిల్ లీకేజీని తగ్గించవచ్చు.
④ మైక్రో-ఆయిల్ సిరీస్ కుట్టు యంత్రానికి మారండి.
పోస్ట్ సమయం: ఫిబ్రవరి-26-2024