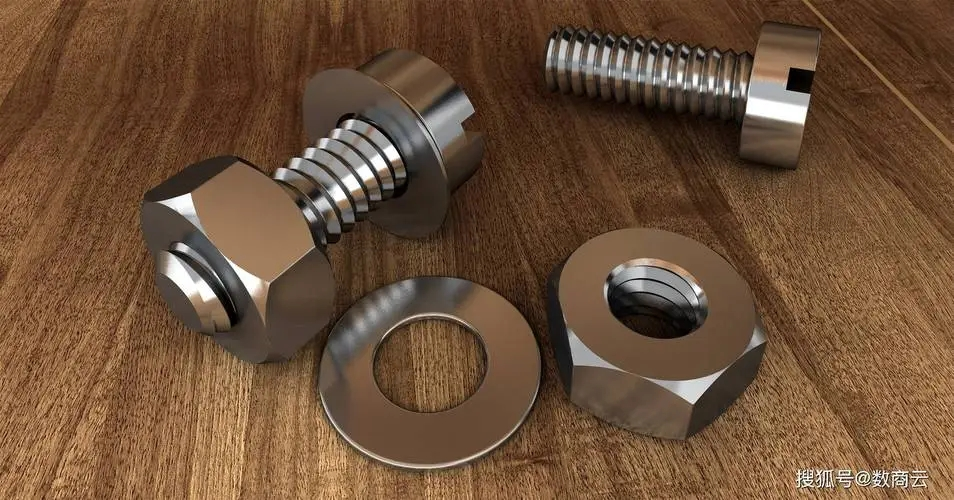
නිෂ්පාදනයේ පෙනුමේ ගුණාත්මකභාවය සංවේදී ගුණාත්මක භාවයේ වැදගත් අංගයකි.පෙනුමේ ගුණාත්මක භාවය සාමාන්යයෙන් අදහස් වන්නේ දෘශ්යමය වශයෙන් නිරීක්ෂණය කළ හැකි නිෂ්පාදනයේ හැඩය, වර්ණ ස්වරය, ග්ලෝස්, රටාව යනාදී ගුණාත්මක අංග වේ.නිසැකවම, ගැටිති, සීරීම්, ඉන්ඩෙන්ටේෂන්, සීරීම්, මලකඩ, පුස්, බුබුලු, සිදුරු, වලවල්, මතුපිට ඉරිතැලීම්, දිරාපත්වීම, රැළි වැනි සියලුම දෝෂ නිෂ්පාදනයේ පෙනුමේ ගුණාත්මක භාවයට බලපානු ඇත.මීට අමතරව, පෙනුම නිෂ්පාදනවල බොහෝ ගුණාත්මක සාධක නිෂ්පාදන කාර්ය සාධනය, ආයු කාලය සහ අනෙකුත් අංශ කෙරෙහි සෘජුවම බලපායි.සිනිඳු මතුපිටක් සහිත නිෂ්පාදන ශක්තිමත් මලකඩ ප්රතිරෝධය, අඩු ඝර්ෂණ සංගුණකය, හොඳ ඇඳුම් ප්රතිරෝධය සහ අඩු බලශක්ති පරිභෝජනය.
නිෂ්පාදනයේ පෙනුමේ ගුණාත්මකභාවය තක්සේරු කිරීම යම් ආත්මීයත්වයක් ඇත.හැකිතාක් දුරට වෛෂයික විනිශ්චයන් සිදු කිරීම සඳහා, කාර්මික නිෂ්පාදන තත්ත්ව පරීක්ෂාවේදී පහත සඳහන් පරීක්ෂණ ක්රම බොහෝ විට භාවිතා වේ.
(1)සම්මත සාම්පල කණ්ඩායම් ක්රමය.සුදුසුකම් ලත් සහ නුසුදුසු සාම්පල සම්මත සාම්පල ලෙස පූර්ව තෝරා ගන්න, එහිදී සුදුසුකම් නොලබන සාම්පලවල විවිධ ප්රමාණයේ බරපතලකම සහිත විවිධ දෝෂ තිබේ.
බොහෝ පරීක්ෂකවරුන් (ඇගයුම්කරුවන්) විසින් සම්මත සාම්පල නැවත නැවතත් නිරීක්ෂණය කළ හැකි අතර නිරීක්ෂණ ප්රතිඵල සංඛ්යානමය වශයෙන් විශ්ලේෂණය කළ හැකිය.සංඛ්යානමය ප්රතිඵල විශ්ලේෂණය කිරීමෙන් පසු, කුමන දෝෂ කාණ්ඩ නිසි ලෙස අර්ථ දක්වා නොමැතිද යන්න තීරණය කළ හැකිය;ප්රමිතීන් පිළිබඳ ගැඹුරු අවබෝධයක් නොමැති පරීක්ෂකවරුන් කවරේද;කුමන පරීක්ෂකවරුන්ට අවශ්ය පුහුණුව සහ විචක්ෂණ හැකියාවන් නොමැත.
(2)ඡායාරූප නිරීක්ෂණ ක්රමය.ඡායාරූපකරණය හරහා, සුදුසුකම් ලත් පෙනුම සහ අවසර ලත් දෝෂ සීමාවන් ඡායාරූප මගින් නිරූපණය කළ හැකි අතර, විවිධ පිළිගත නොහැකි දෝෂවල සාමාන්ය ඡායාරූප සංසන්දනාත්මක පරීක්ෂාව සඳහා ද භාවිතා කළ හැකිය.
(3)දෝෂ විස්තාරණ ක්රමය.දෝෂ වල ස්වභාවය සහ බරපතලකම නිවැරදිව නිර්ණය කිරීම සඳහා නිෂ්පාදනයේ මතුපිට විශාල කිරීමට සහ නිරීක්ෂණය කරන ලද මතුපිට දෝෂ සෙවීමට විශාලන වීදුරුවක් හෝ ප්රොජෙක්ටරයක් භාවිතා කරන්න.
(4)අතුරුදහන් දුර ක්රමය.නිෂ්පාදන භාවිත අඩවියට ගොස් නිෂ්පාදනයේ භාවිත තත්ත්වයන් පරීක්ෂා කර නිෂ්පාදනයේ භාවිත තත්ත්වය නිරීක්ෂණය කරන්න.ඉන්පසු නිෂ්පාදනයේ සත්ය භාවිත කොන්දේසි අනුකරණය කරන්න, පරීක්ෂා කිරීම සඳහා නිරීක්ෂණ කොන්දේසි ලෙස අනුරූප වේලාව, නිරීක්ෂණ දුර සහ කෝණය සඳහන් කරන්න.යම් නිෂ්පාදනයක පෙනුමේ දෝෂයක් නිශ්චිතව දක්වා තිබේ නම්, එය මීටරයක දුර සිට තත්පර 3 ක් ඇතුළත නොපෙනෙන තාක් කල්, එය සුදුසුකම් ලෙස සලකනු ලැබේ, එසේ නොමැති නම් එය නුසුදුසු ලෙස සලකනු ලැබේ.මෙම ක්රමය ප්රමිතීන් සැකසීමට සහ විවිධ වර්ගවල සහ පෙනුමේ දෝෂවල බරපතලකම මත අයිතමය අනුව අයිතම පරීක්ෂා කිරීමට වඩා පහසු සහ අදාළ වේ.
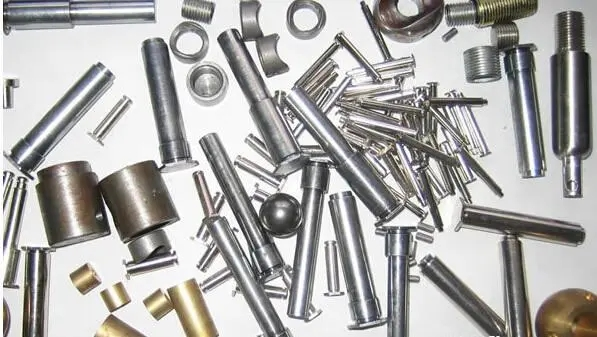
උදාහරණ: සංරචක මත ගැල්වනයිස් කරන ලද ආලේපනයේ පෙනුමේ තත්ත්ව පරීක්ෂාව.
①පෙනුමේ ගුණාත්මක අවශ්යතා.ගැල්වනයිස් කරන ලද ආලේපනයේ පෙනුමේ ගුණාත්මක භාවයට අංශ හතරක් ඇතුළත් වේ: වර්ණය, ඒකාකාරිත්වය, අවසර ලත් දෝෂ සහ පිළිගත නොහැකි දෝෂ.
වර්ණ.උදාහරණයක් ලෙස, ගැල්වනයිස් කරන ලද තට්ටුව සුළු බීජ් පැහැයක් සහිත ලා අළු පැහැයක් විය යුතුය;ආලෝකයට නිරාවරණය වීමෙන් පසුව, ගැල්වනයිස් කරන ලද තට්ටුව රිදී සුදු පැහැයක් සහ යම් දිලිසීමක් සහ ලා නිල් පැහැයක් ගනී;පොස්පේට් ප්රතිකාර කිරීමෙන් පසු ගැල්වනයිස් කරන ලද තට්ටුව ලා අළු සිට රිදී අළු දක්වා විය යුතුය.
ඒකාකාරී බව.ගැල්වනයිස් කරන ලද ස්තරය සිහින්ව ස්ඵටිකීකරණය කරන ලද, ඒකාකාර සහ අඛණ්ඩ මතුපිටක් තිබීම අවශ්ය වේ.
අඩුපාඩු වලට ඉඩ දෙන්න.උදාහරණයක් ලෙස, සුළු ජල පැල්ලම්;කොටස් ඉතා වැදගත් වන අතර, මතුපිට සුළු සවි කිරීම් සලකුණු ඇත;එකම කොටසෙහි වර්ණය හා ග්ලෝස් වල සුළු වෙනස්කම් ඇත.
අඩුපාඩු වලට ඉඩ නොදේ.උදාහරණයක් ලෙස: බිබිලි ඇතිවීම, පීල් කිරීම, පිළිස්සීම, නූඩ්ලේෂන් සහ ආෙල්පන වළවල්;ඩෙන්ඩ්රිටික්, ස්පොන්ජ් වැනි සහ ඉරි සහිත ආලේපන;අපිරිසිදු ලුණු පැල්ලම් ආදිය.
②පෙනුම පරීක්ෂා කිරීම සඳහා නියැදීම.වැදගත් කොටස්, තීරනාත්මක කොටස්, විශාල කොටස් සහ 90 ට අඩු කණ්ඩායම් ප්රමාණය සහිත සාමාන්ය කොටස් සඳහා, පෙනුම 100% පරීක්ෂා කළ යුතු අතර අනුකූල නොවන නිෂ්පාදන ඉවත් කළ යුතුය;කෑලි 90 ට වඩා වැඩි කාණ්ඩ ප්රමාණයක් සහිත සාමාන්ය කොටස් සඳහා, නියැදි පරීක්ෂාව සිදු කළ යුතු අතර, සාමාන්ය පරීක්ෂණ මට්ටම II සහ සුදුසුකම් ලත් තත්ත්ව මට්ටම 1.5% කි.2-12 වගුවේ දක්වා ඇති සාමාන්ය පරීක්ෂණ නියැදි සැලැස්මට අනුව පරීක්ෂාව සිදු කළ යුතුය.සුදුසුකම් නොලබන කණ්ඩායමක් සොයාගත් විට, කණ්ඩායම 100% පරීක්ෂා කිරීමට, නුසුදුසු නිෂ්පාදන ඉවත් කිරීමට සහ නැවත පරීක්ෂා කිරීම සඳහා ඉදිරිපත් කිරීමට අවසර ඇත.
③පෙනුම පරීක්ෂා කිරීමේ ක්රම සහ තත්ත්ව ඇගයීම.දෘෂ්ය පරීක්ෂාව පෙනුම පරීක්ෂා කිරීම සඳහා ප්රධාන ක්රමය වන අතර, අවශ්ය නම්, පරීක්ෂා කිරීම සඳහා 3-5 වතාවක් විශාලන වීදුරු භාවිතා කළ හැකිය.පරීක්ෂා කිරීමේදී, 300 lux ට නොඅඩු ආලෝකයක් සහිතව, පරාවර්තනයකින් තොරව ස්වභාවික විසිරුණු ආලෝකය හෝ සුදු සම්ප්රේෂණය කරන ලද ආලෝකය භාවිතා කළ යුතු අතර, කොටස් සහ මිනිස් ඇස අතර දුර ප්රමාණය මිලිමීටර් 250 කි.
කණ්ඩායම් ප්රමාණය 100 නම්, කෑලි 32 ක නියැදි ප්රමාණය නිස්සාරණය කළ හැකිය;මෙම කොටස් 32 දෘෂ්ය පරීක්ෂාවේදී, ඉන් දෙකකින් ආලේපනයේ බිබිලි සහ පිළිස්සුණු සලකුණු ඇති බව සොයා ගන්නා ලදී.අනුකූල නොවන නිෂ්පාදන සංඛ්යාව 2 ක් වූ බැවින්, මෙම කොටස් සමූහය අනුකූල නොවන බව තීරණය විය.
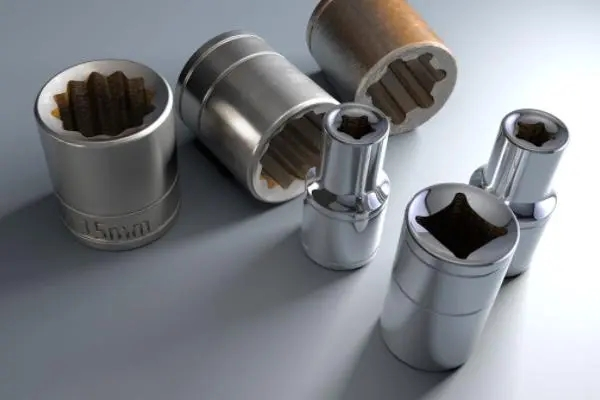
පසු කාලය: අප්රේල්-03-2024