There are many types of furniture, such as solid wood furniture, wrought iron furniture, panel furniture, and so on. Many furniture items require consumers to assemble them themselves after purchase. Therefore, when inspectors need to inspect assembled furniture, they need to assemble the furniture on site. What are the equipment steps for disassembling and assembling furniture, how to operate it on site, and what are the precautions.
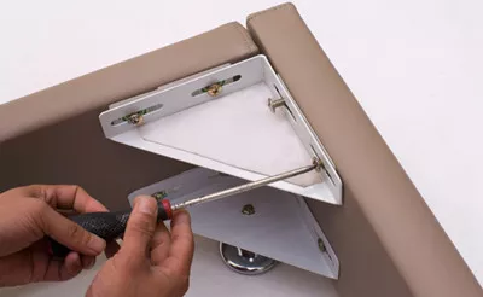
1.On site assembly inspection quantity
1)The inspector must independently assemble at least one set of products according to the assembly manual. If the product size is too large and requires the help of factory personnel, it is necessary to ensure that the connection and matching parts are installed and operated by the inspector themselves.
2)The assembly of other products can be completed by factory personnel, but it needs to be completed under the full on-site supervision of the inspector. It is important to inspect the entire process of product assembly, rather than just focusing on the final result of assembly. Therefore, during the equipment process, the inspector cannot leave the assembly site, and the quantity of equipment depends on the inspection (WI) requirements.
2.On site assembly steps and precautions
1)On site equipment must strictly follow the assembly instructions provided by the product. During the assembly process, check whether the steps in the assembly instructions are correct, whether each component meets technical requirements, whether it fits tightly, whether the hole position is correct, whether the product is firm, and whether external tools are needed (generally not allowed, specific requirements depend on the instructions)
2)Before assembly, it is important to identify the number of pieces of the product, open the cardboard box for packaging, place the hardware package in a separate location and count it to avoid loss or mixing with accessories from other products.
3)First, check whether the number and size of components match the quantity indicated in the manual. During assembly, be careful not to replace unsuitable parts.
4) Carefully read the assembly manual, first separate the main components in order of assembly, and visit the boards separately for matching installation. It is best to take photos of these boards uniformly.
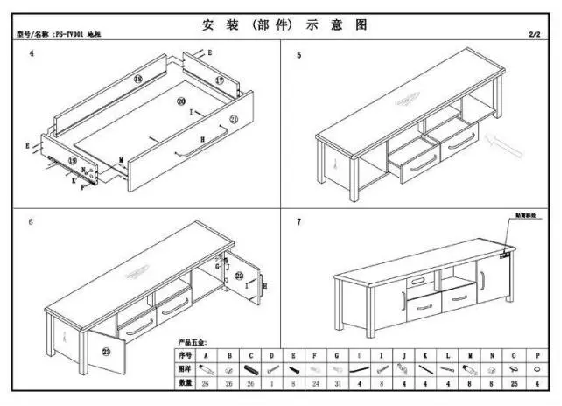
5)Prepare installation tools such as screwdrivers, wrenches, etc., and strictly follow the assembly steps in the product assembly manual during the assembly process. Inspectors need to pay special attention: factory personnel often rely on experience during assembly and fail to fully follow the steps in the equipment manual. This practice cannot verify whether the equipment manual is reasonable and complete. If this situation is found, it should be stopped/corrected immediately. It is best to install one unit at a time, and not multiple units at the same time, to avoid inadequate supervision.
6) Generally speaking, the assembly process of most products can be divided into four stages:
The first step is to form the skeleton of the product. During this process, attention should be paid to whether the connection holes of the skeleton are correct, whether the installation of bolts and other fasteners is smooth, whether the connectors are locked, and whether the gaps of the skeleton are uniform and consistent.
The second step is to install fixed components that strengthen the structure on the skeleton. During this process, attention should be paid to hardware accessories, especially screws, which should not be missed. All components and fasteners should be placed on the frame, and the connection holes should be checked for suitability. It is important to note that screw hole misalignment often occurs during this process.
The third step is to install guiding devices or hinge connected moving parts in corresponding positions. It is important to note that furniture components can be disassembled and assembled multiple times without any damage issues. In this process, attention should be paid to whether these accessories have loose screw holes or damaged parts after a single connection.
The fourth part is to install minor or decorative components or accessories. During this process, attention should be paid to whether the screw length meets the requirements, whether the decorative accessories can be reinforced tightly, whether the hole position is appropriate when locking the screw, and whether the product should not be scratched or the accessories should not be loose.
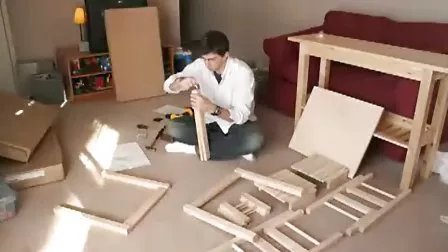
Frequently asked questions
1. Lack of components in the product, especially hardware accessories in small packaging
2. The hole position does not meet the requirements, mainly including incorrect connection hole position, small hole, too shallow or too deep hole, direction deviation, etc
3. The accessory holes on the board are filled with paint, and the hardware cannot be smoothly inserted
4. Hardware accessories cannot be locked tightly, and the product is not secure
5. When locking hardware accessories, the components may deform, crack, or be damaged
6. Functional moving parts cannot be pushed or pulled smoothly
7. Damaged connectors and rust stains on the surface of hardware accessories
8. Excessive or uneven gaps between components during assembly
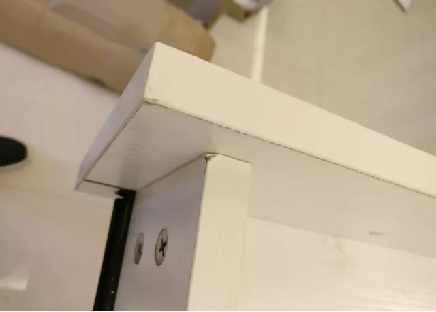
Quality requirements and inspection methods for products
1. Inspection method
Tool measurement, visual inspection, hand touch, and inspection of products according to product assembly technical requirements and drawing dimensions and shapes
2. Detection distance
Should be under natural light or approximate natural light (e.g. 40W fluorescent lamp), with a visual range of 700-1000mm
3. Focus of appearance inspection
1) The welding, riveting, mortise and tenon joints used for fixing components should not be loose
2) Screws and hardware connections must not be loose
3) The surface of hardware accessories has no scratches, the plating (coating) layer is firm, and there is no peeling or rusting
4) Load bearing components and moving parts must not have cracks, knots, insect holes, or other defects
5) The moving parts should be firmly and reliably connected, not falling off on their own, and should be flexible and easy to use
6) Metal fittings should have no cracks or scars
7) There should be no desoldering, virtual welding, or welding penetration at the welding site
8) The welded parts should be free of pores, weld nodules, and spatter
9) The riveted parts should be riveted smoothly without hammer marks
10) The coating should be free of burns, bubbles, pinholes, cracks, burrs, and scratches
11) The coating of metal parts should have no exposed bottom, unevenness, obvious sagging, lumps, wrinkles, or flying paint
12) No scratches or scratches on the surface of the finished product
13) The overall structure of the product is firm, balanced on the ground, and there is no looseness in the components when shaken. The joints are tight and there are no obvious gaps
14) The lenses and glass cabinet doors are clean without any adhesive marks, and the bonding or joints are tight and firm
15) Hardware accessories that are frequently opened, such as hinges, retractables, drawer slides, etc., require flexible opening and closing
16) The solid wood components have no signs of decay, insect holes, fractures, etc., and the color and wood grain direction are consistent. The moisture content meets the requirements
17) The coating of wooden parts should not have wrinkles or paint leakage: the coating or coating of metal parts should not have peeling, embroidery, or paint leakage
18) The coating on wooden parts should be flat and smooth, without scratches, white spots, bubbles, sagging, and obvious color differences
19) The panel components are free from hollow, loose, insect infested, cracked, chipped, scratched, nailed out, pierced, and other phenomena
20) The surface color should be consistent, whether comparing a single piece in different positions or comparing the entire system, the color should be consistent
21) There are no obvious tool marks on the surface, such as knife marks, drag marks, fragmentation, cracking, sand black, and sinking
22) The hinge should not be bent or excessively raised, and it is not allowed to adjust the door by bending the hinge to maintain its flatness
23) Glass and mirrors must be installed without shaking or loosening
24) The product has no debris, sharp protrusions, burrs, glue marks, burnt black, or excessive spraying
25) The overall size of the finished product meets the requirements of the drawing, and the external dimensions are within the allowable size tolerance range
Common hardware accessories for dismantling and assembling furniture
Hardware accessories are generally used to fix and connect the structure when disassembling furniture. Common connectors in furniture include hinges, connectors (eccentric or permanent), drawer slides, sliding door slides, handles, locks, locking pins, door suction cups, partition supports, hanging clothes sticks, pulleys, legs, bolts, wooden screws, wooden tenons, round nails, etc.
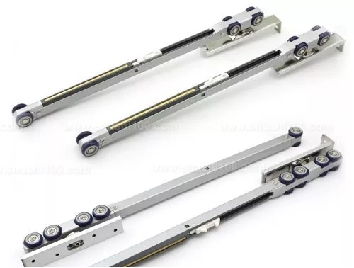
1. Hinge
Hinges are the main structures that connect two moving parts, mainly used for opening and closing cabinet doors, divided into exposed hinges and concealed hinges
1) Ming hinge
Hinges are usually only hinges, and when installed, the pin part of the hinge is exposed to the surface of the furniture. Hinges can be used for built-in doors and folding doors.
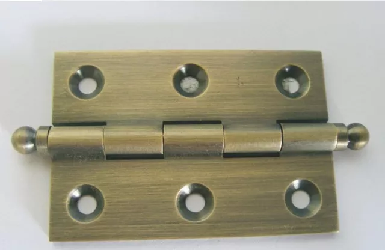
2) Concealed hinge
The concealed hinge rotates by the connecting rod and is hidden inside the furniture during installation without leakage
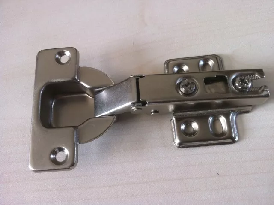
2. Connection components
Connector, also known as fixed connector, has a direct impact on the structure and firmness of furniture products. It is mainly used for connecting side panels, horizontal panels, and back panels of cabinet furniture to fix furniture panels. The connecting rod includes eccentric connectors and permanent connectors.
1) Eccentric connector
Using an eccentric distance, connect the horizontal plate to the side plate, such as the floor and side plate, and the bottom plate can be installed from the top or side.
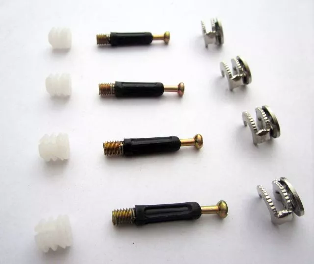
2) Permanent connectors
It consists of two parts: a screw and a sleeve with a spring steel plate. After pressing the connection by hand, the object is permanently connected, characterized by a very strong connection.
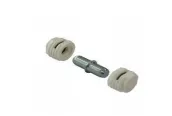
3. Drawer slide
The drawer slide rails are generally made of iron baking paint or iron galvanized materials. According to the different methods in East China, they can be divided into pulley type or ball type. According to the distance from the drawer to the cabinet, they can be divided into single section rails, double section rails, and three section rails.
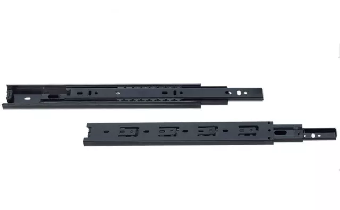
4. Bolt
A type of fastener consisting of a head and a bolt (a cylindrical body with external threads), which needs to be matched with the curtain and is used to tighten and connect two parts with through holes. This connection form is called bolt connection.
5. Circular tenon
One of the commonly used assembly and connection accessories for panel furniture, which is shaped like a round rod and is generally made of wood. In the disassembly and assembly of furniture, wooden tenons play a positioning role, with commonly used diameters of 6mm, 8mm, 10mm, and 12mm, and lengths of 20mm, 25mm, 30mm, 35mm, 40mm, and 50mm.
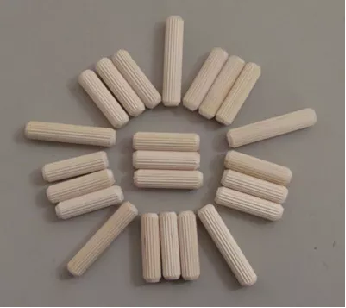
6. Other connectors
Screws, self tapping screws, nuts, washers, spring washers, cylindrical nuts, double ribbed nuts, handles, etc.
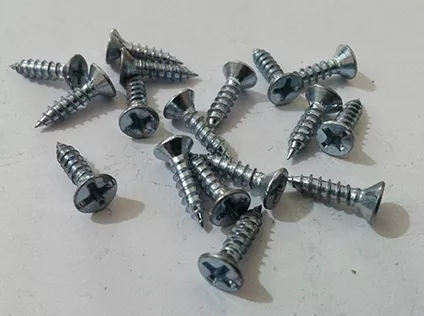
Post time: May-09-2024